About new 3D printer filaments
In a range of filaments, which we offer for 3D printers, there are 2 new very interesting materials:
-
HTW P-Carbon - filament based on modified polyurethane with addition of carbon fiber, which increase rigidity and durability. This material exhibits good interlayer adhesion. It proves itself as good material for printing of loaded nodes and gears, and it is an excellent alternative to nylon.
Recommended print parameters:
- Extruder nozzle temperature: 230-240 °С;
- Table temperature 80-90: °С;
- Nozzle diameter from: 0.3 mm;
- Thermostability from -50 °С to 130 °С (elasticity strongly rises in a renge from 90 °С to 130 °С).
-
HTW SBS+ is a filament, made of modified SBS plastic, laced with special additions, which increase hardness, abrasion resistance, thermostability and lower shrinkage. It features good interlayer adhesion. HTW SBS+ plastic could be considered as a replacement to ABS filament for printing of functional prototypes.
Recommended print parameters:
- Nozzle temperature 240-260 °С;
- Table temperature 80-90 °С;
- Nozzle diameter from 0.2 mm;
- Thermostability up to 85 °С.
For the purpose of testing these materials it was decided to print a small traction mechanism - winch arrangement. First the design was done using a CAD software, the model of geared motor was requested from a seller company smd.ee.
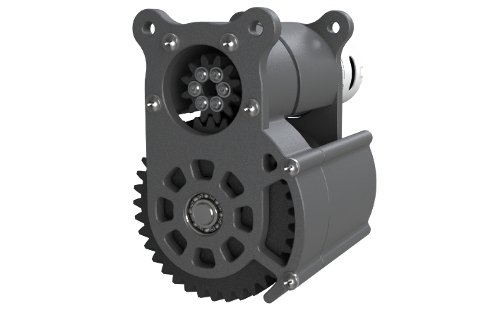
As this model doesn't have small parts, the nozzle diameter 0.5 mm was chosed, it decreases printing time and improves interlayer adhesion. To print gears and geared motor mounting flange the filament HTW P-Carbon was used. For base member HTW SBS+ filament was used. All parts were printed on a SCARA 3D printer SkyOne.
For the purpose of secure fasten of a driving gear at the geared motor shaft a compression coupling (made from a usual flexible coupling) was used.
A 10 mm shaft was pressed into a wheel hub, this shaft will be set into bearings 6900RS series. Then a kevlar was winded up.
Some photos of printing and assembling process:
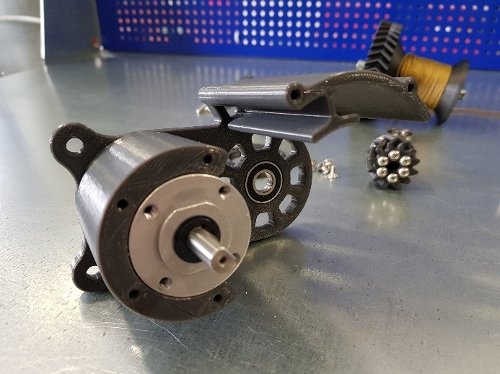
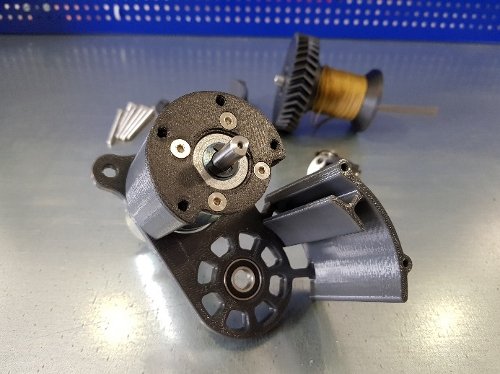
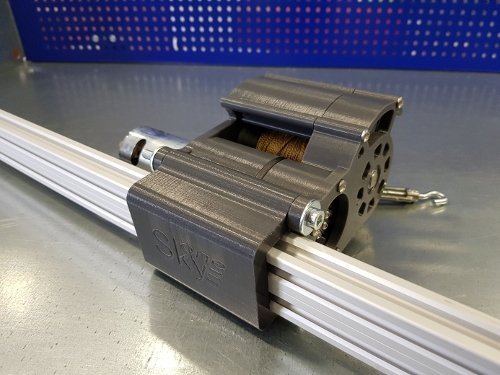
For working capacity testing a usual induction geared motor (about 20 kg mass) was used. The winch withstanded the load, but the kevlar thread is fast-wearing. Afer 15 cycles of lift/descent it became obvious raveled. The gears are without any evidence of working. The testing will be continued after the kevlar will be replaced by something more reliable.
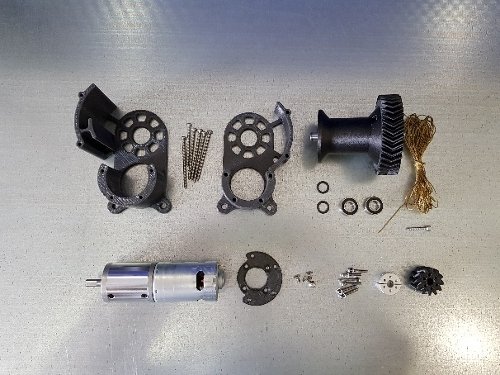
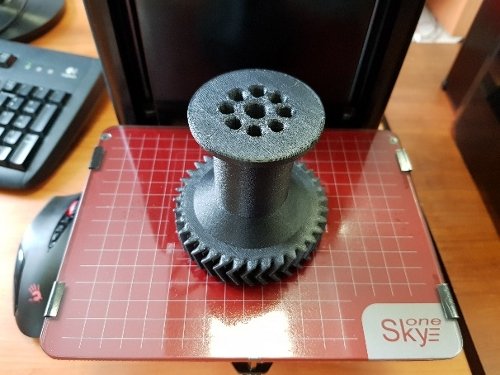
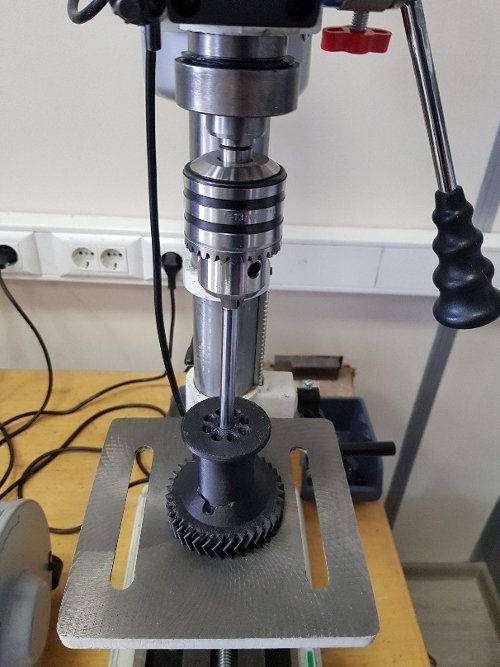
