Printing of a protective elastic shell at 3D printer SkyOne
Protective elastic shells - corrugated tubes, screens, sleeve gaskets are widely used both in industry and in our everyday life. Single-part and small volume productions are questions of present interest. Traditionally rubber and rubberlike goods are produced by the way of compression moulding and vulcanization in a compression mould. However, it is to be noted that this method of manufacturing has an essential demerit. It is that usually vulcanization process occurs on low productive presses, vulcanization time for some details riches up to an hour. High pice of a complex compression mould is another factor, which limits potentialities.
Modern additive technologies make it possible to meet challenges of small volume manufacturing without usage of compression moulds, and productiveness is comparable with a traditional technology.
Let's take a look at some examples of 3D printing with FLEX material.
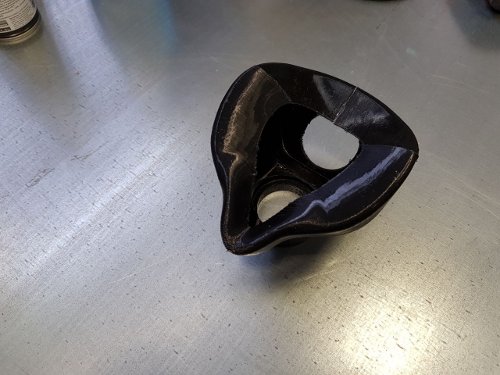
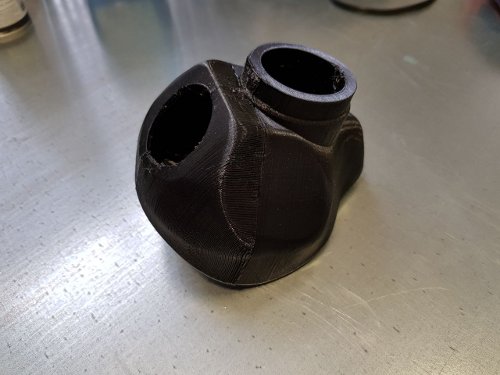
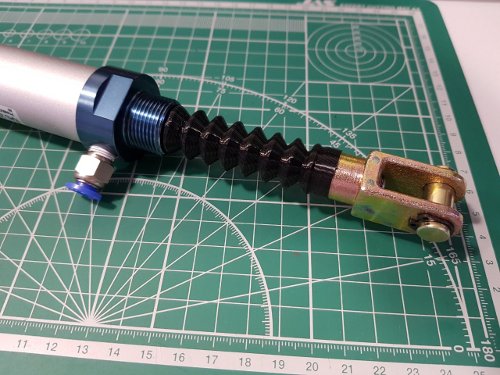
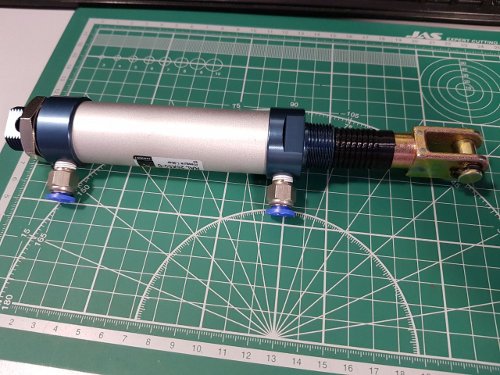
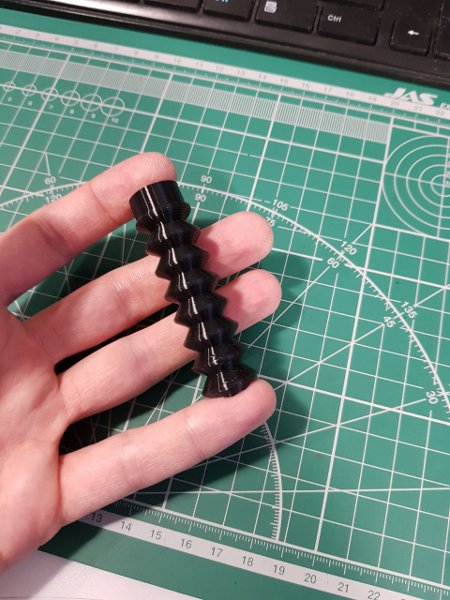
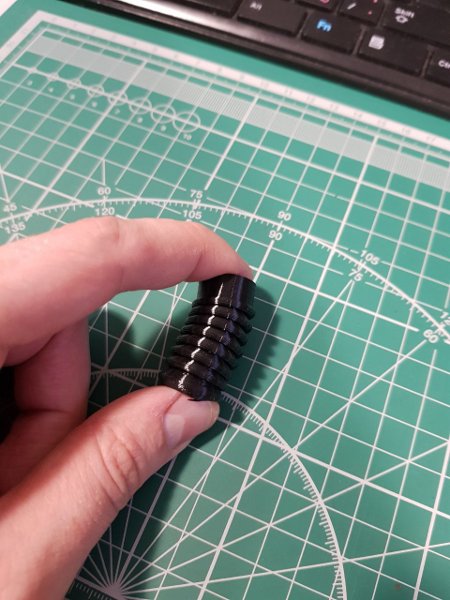
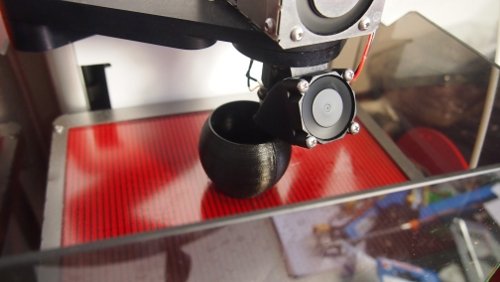
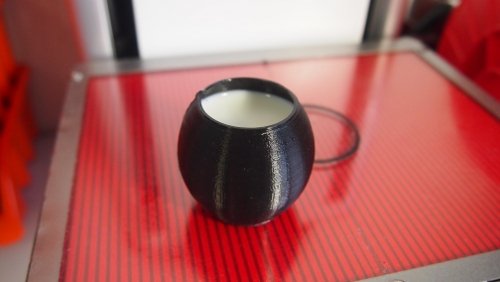
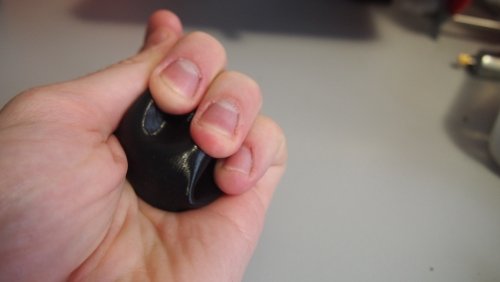
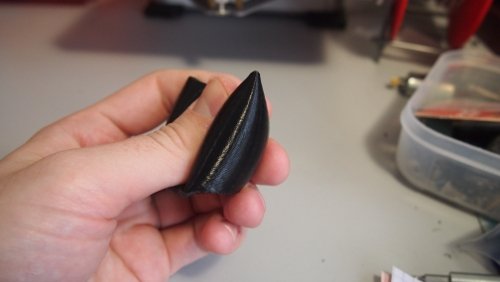
An obvious advantage of 3D printing with elastic material is time saving and cost saving as it is no need to produce a press mould. In most cases 3D printing time of details below 100 g weight is about 1-2 hours, and a press mould is not required. A final product strength is specified by ability of material layers to sinter. As it is seen from the video, it is highly competitive with goods, produced by vulcanization process. Elastic shells are printed according a method "continuous filament" spirally, it allows avoiding of joints in every of layers and essentially eliminate possibility of arising of leak-tight points. A high class stepper motor driver in the extruder with microstepping 1/128 allows for smooth and uniform feed of elastic material.
As an conclusion it should be noted, that the price of a press mould for elastic shell manufacturing, which is shown in the example 2, is notably higher, than SkyOne 3D printer price.