Plastic conductor, printed on 3D printer SkyOne
Here is an experience of using 3D printer for solution of practical tasks.
It is time to think of winterising of balconies when the weather is getting colder. To make the floor warmer it is needed to fix a frame from wooden floor beams. And it is better to drill the beams. So here we are in need of a help of the 3D printer.
A plastic conductor was modeled and printed from @HTW SBS+ filament in order to drill the holes in the center of beams and keep perpendicular alignment. The nozzle diameter is 0.8, layer height is 0.2, infill dencity is 90%.
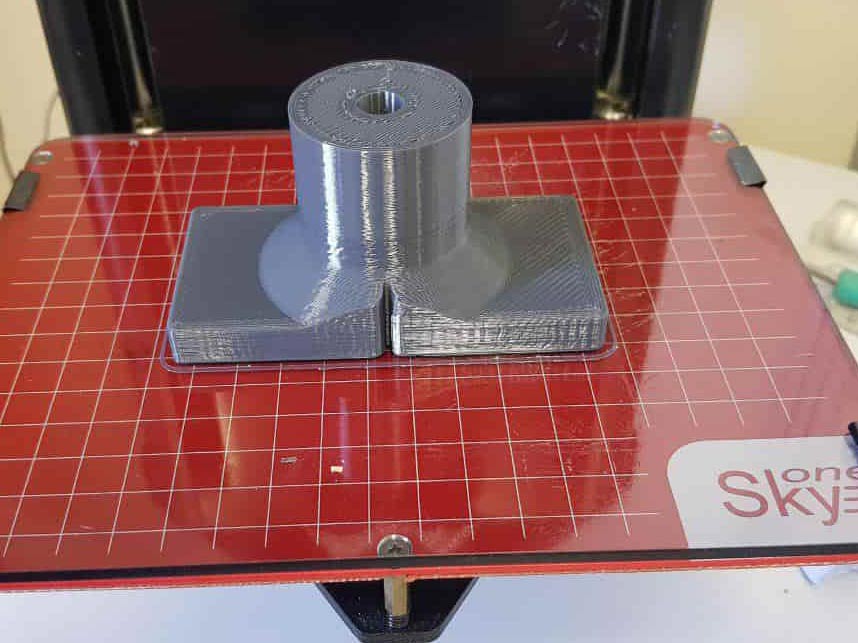
The hole diameter is 10.5 mm, it is 0.5 mm more, than diameter of the drill. So it decreases a risk of touching and heating of plastic. This model has fastening lug for clamping and grooving for centering align a line.
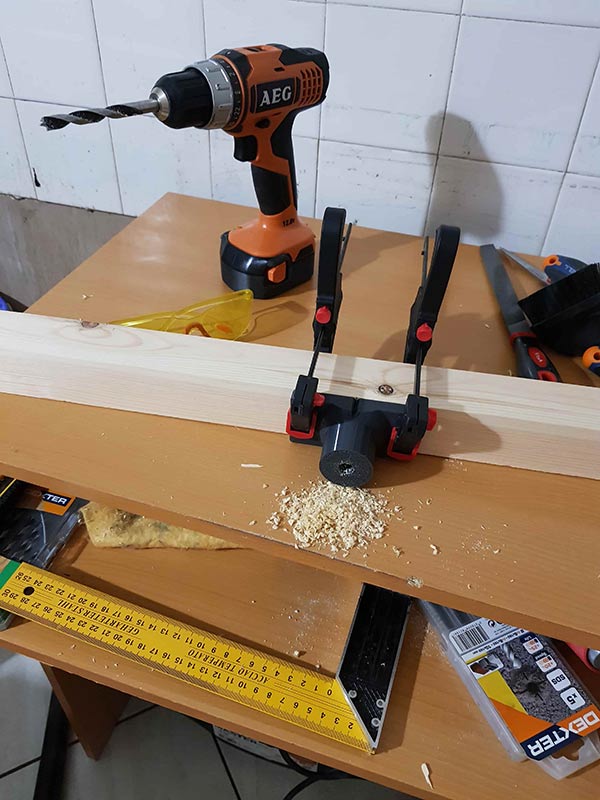
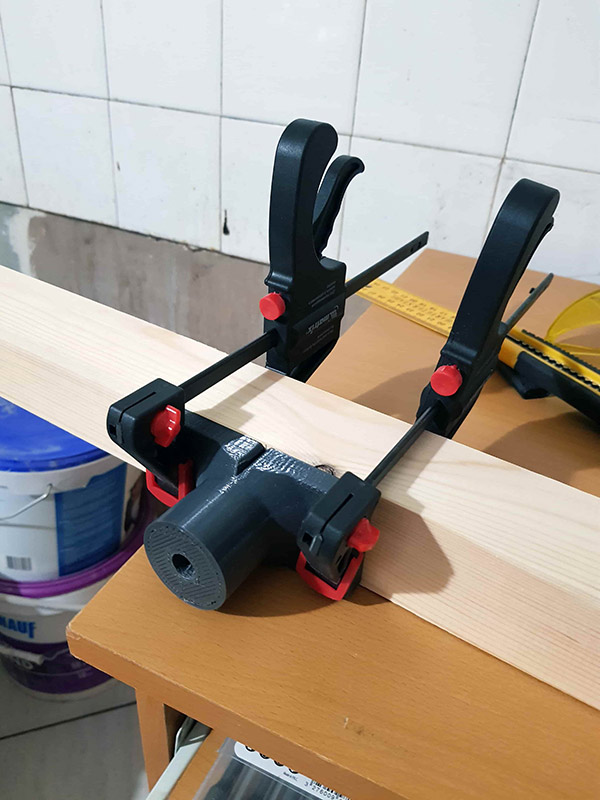

The drilling was made vertically to provide satisfied chip clearance Aftre 15 iterations of drilling (through hole 10 mm diameter in a beam 50x50 mm), wearing of the conductor turned out 1.5 mm. As the height of the conductor is 50 mm, we have got a deviation from the target point 2 mm. Such deviation is acceptable for the further drilling. But we have 15 holes more to drill, so it is better to print out one more conductor. The second conductor was made from graphite-reinforced filament HTW P-Carbon (HTW SBS+ could be suitable as well).
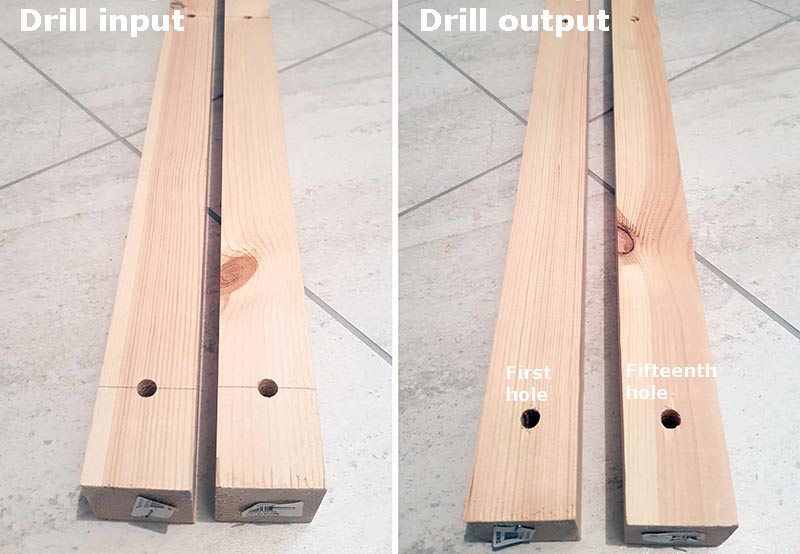
All advantages of 3D printing in this case is that it was so easy to create a field-specific accessory product, which is suitable for specific geometry and dimensions of the beams and takes into account usage of the specific clamps.
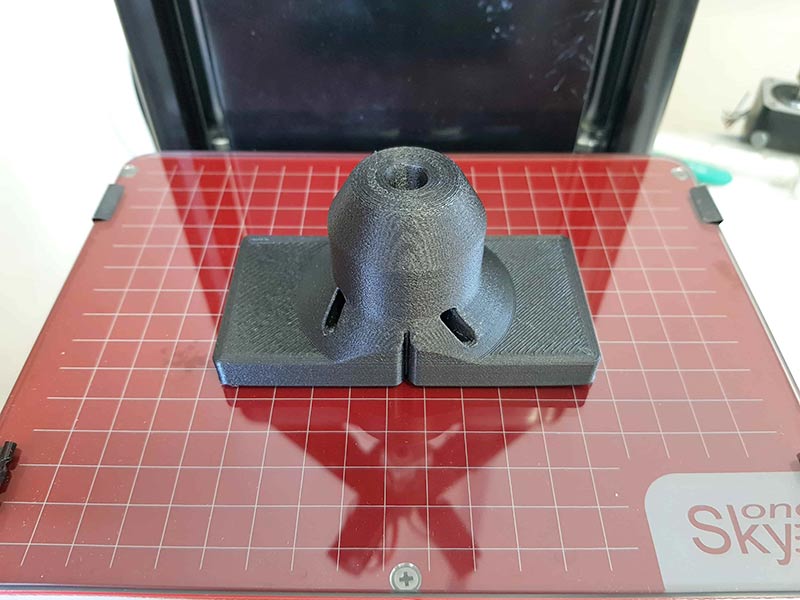